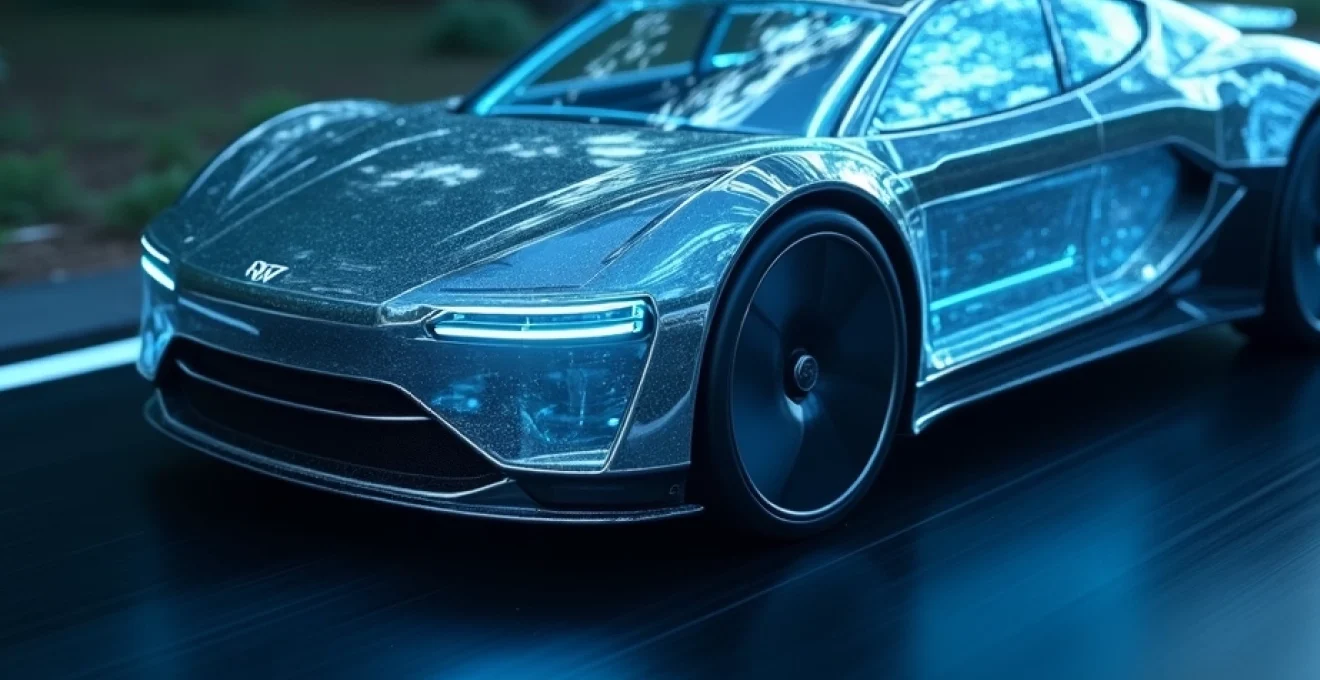
Lithium batteries have become the cornerstone of the electric vehicle (EV) revolution, powering the transition from fossil fuel-dependent transportation to a cleaner, more sustainable future. These powerful energy storage devices are not just components; they are the beating heart of modern EVs, enabling unprecedented range, performance, and efficiency. As the automotive industry races towards electrification, the continuous evolution of lithium battery technology is shaping the landscape of personal transportation and urban mobility.
Lithium-ion battery chemistry and its impact on EV performance
The chemistry behind lithium-ion batteries is a critical factor in determining the performance, range, and safety of electric vehicles. As manufacturers strive to create more efficient and powerful EVs, advancements in battery chemistry play a pivotal role in pushing the boundaries of what's possible.
Cathode materials: NMC vs NCA technology
Two dominant cathode technologies currently lead the EV battery market: Nickel Manganese Cobalt (NMC) and Nickel Cobalt Aluminum (NCA). Each offers distinct advantages and trade-offs that impact vehicle performance. NMC batteries are known for their balanced approach, offering good energy density, power, and longevity. On the other hand, NCA batteries provide higher energy density but at the cost of slightly reduced stability.
The choice between NMC and NCA often comes down to the specific requirements of the vehicle. For instance, Tesla has long favored NCA chemistry for its high energy density, which contributes to the extended range of their vehicles. However, many other manufacturers opt for NMC due to its more stable thermal properties and longer cycle life.
Advancements in silicon-graphite anodes
While much attention is given to cathode materials, significant progress is also being made in anode technology. Traditional graphite anodes are being enhanced with silicon, a material that can theoretically store ten times more lithium ions than graphite. This advancement holds the promise of dramatically increasing battery capacity without significantly increasing weight or size.
Companies like Sila Nanotechnologies and Amprius are at the forefront of silicon anode development, working on overcoming challenges such as volume expansion during charging. The integration of silicon-graphite anodes could lead to EVs with ranges that rival or exceed those of conventional gasoline-powered vehicles.
Solid-state electrolytes: the future of EV batteries
Perhaps the most exciting development in lithium battery technology is the pursuit of solid-state electrolytes. Unlike conventional lithium-ion batteries that use liquid electrolytes, solid-state batteries employ a solid electrolyte, which could potentially offer higher energy density, faster charging times, and improved safety.
Solid-state technology is still in its early stages, with companies like QuantumScape and Toyota investing heavily in research and development. If successful, solid-state batteries could revolutionize the EV industry, addressing many of the current limitations of liquid electrolyte batteries and potentially doubling the range of electric vehicles.
Energy density improvements in lithium batteries for extended EV range
One of the most critical factors in EV adoption is range anxiety – the fear of running out of power before reaching a charging station. To combat this, manufacturers are focusing intensely on improving the energy density of lithium batteries, allowing for greater range without increasing battery size or weight.
Tesla's 4680 cell design: increasing volumetric energy density
Tesla's innovative 4680 cell design represents a significant leap forward in battery technology. These larger format cylindrical cells offer several advantages over traditional designs. The increased size allows for more active material within the cell, while the "tabless" design improves electrical performance and thermal management.
The 4680 cells are expected to increase volumetric energy density by up to 5 times and power output by 6 times compared to Tesla's previous cells. This improvement translates directly to extended range and enhanced performance for EVs utilizing this technology.
Byd's Blade Battery: optimizing pack-level energy density
Chinese automaker BYD has taken a different approach with its Blade Battery technology. This innovative design uses long, thin lithium iron phosphate (LFP) cells arranged in a blade-like configuration. The Blade Battery optimizes space utilization within the pack, resulting in a volumetric energy density increase of up to 50% compared to conventional LFP batteries.
While LFP chemistry typically offers lower energy density than NMC or NCA, BYD's design compensates for this by maximizing pack-level efficiency. The result is a battery that offers improved safety, longevity, and cost-effectiveness without sacrificing too much in terms of range.
Catl's cell-to-pack technology: eliminating module housings
Contemporary Amperex Technology Co. Limited (CATL), the world's largest EV battery manufacturer, has developed cell-to-pack (CTP) technology that further improves energy density at the pack level. By eliminating the need for module housings and integrating cells directly into the pack, CATL has achieved a 15-20% increase in energy density.
This technology not only improves range but also simplifies manufacturing and reduces costs. CATL's CTP batteries are already being used in vehicles like the Tesla Model 3 produced in China, demonstrating the real-world applicability of this innovation.
Fast-charging capabilities of lithium batteries in EVs
As electric vehicles become more prevalent, the demand for faster charging times grows. Lithium battery technology is evolving to meet this challenge, with several innovations aimed at reducing charging times and improving the overall EV ownership experience.
800V architecture: Porsche Taycan and Hyundai IONIQ 5
One of the most significant advancements in fast-charging technology is the adoption of 800V architecture. Pioneered by Porsche in the Taycan and later implemented by Hyundai in the IONIQ 5, this high-voltage system allows for much faster charging rates compared to the more common 400V systems.
With 800V architecture, EVs can charge at rates of up to 350 kW, potentially adding hundreds of kilometers of range in just 15-20 minutes. This dramatic reduction in charging time brings EVs closer to the refueling convenience of traditional gasoline vehicles, addressing one of the primary concerns of potential EV adopters.
Thermal management systems for rapid charging
Effective thermal management is crucial for enabling fast charging without compromising battery life or safety. Advanced cooling systems, such as those employing liquid coolants, help dissipate heat generated during rapid charging.
Tesla's SuperCharger network, for instance, utilizes sophisticated thermal management to maintain optimal battery temperature during fast charging sessions. This allows for sustained high charging rates without risking damage to the battery cells.
Battery preconditioning strategies
To further optimize fast charging, many EVs now employ battery preconditioning strategies. This involves warming up the battery to its ideal operating temperature before reaching a fast-charging station. Preconditioning ensures that the battery can accept the maximum charging rate as soon as it's connected, minimizing overall charging time.
For example, when a Tesla driver navigates to a Supercharger station, the vehicle automatically begins preconditioning the battery. This proactive approach maximizes the effectiveness of fast-charging sessions, providing a seamless experience for the user.
Lithium battery lifecycle and sustainability in electric vehicles
As the EV market grows, so does the importance of addressing the environmental impact of lithium battery production and disposal. The industry is making significant strides in improving the sustainability of EV batteries throughout their lifecycle.
Cobalt-free chemistries: LFP batteries in Tesla Model 3
Cobalt, a key component in many lithium-ion batteries, has been a source of ethical and environmental concerns due to its mining practices. In response, manufacturers are developing cobalt-free chemistries, with lithium iron phosphate (LFP) batteries gaining traction.
Tesla has begun using LFP batteries in its standard range Model 3 vehicles produced in China. While LFP batteries typically offer lower energy density, they compensate with longer lifespans, improved safety, and lower costs. This shift towards cobalt-free chemistries represents a significant step towards more sustainable EV battery production.
Recycling processes: redwood materials and Li-Cycle
As the first generation of mass-market EVs reaches the end of their lifespans, battery recycling is becoming increasingly important. Companies like Redwood Materials, founded by former Tesla CTO JB Straubel, are developing innovative processes to recycle lithium-ion batteries and recover valuable materials.
Similarly, Li-Cycle has created a hub-and-spoke model for battery recycling, with regional spoke facilities that shred batteries and a central hub that extracts individual elements. These recycling efforts not only reduce waste but also help secure a domestic supply of critical battery materials, reducing reliance on mining and international supply chains.
Second-life applications: stationary energy storage
Even after an EV battery is no longer suitable for automotive use, it often retains 70-80% of its original capacity. These "second-life" batteries can be repurposed for stationary energy storage applications, such as grid stabilization or residential solar systems.
Automakers like Nissan and BMW have implemented programs to reuse EV batteries in this way, extending the useful life of the batteries and improving the overall sustainability of electric vehicles. This approach not only reduces waste but also provides a cost-effective solution for energy storage needs.
Battery management systems (BMS) for optimal lithium battery performance
The sophistication of battery management systems plays a crucial role in maximizing the performance, longevity, and safety of lithium batteries in electric vehicles. Advanced BMS technologies are continuously evolving to meet the demands of modern EVs.
Cell balancing techniques in multi-cell packs
One of the key functions of a BMS is to ensure that all cells within a battery pack maintain similar voltage levels. This process, known as cell balancing, is critical for maximizing battery capacity and lifespan. Modern BMSs employ advanced algorithms to actively balance cells, transferring charge between cells to maintain optimal performance across the entire pack.
For example, Tesla's BMS uses a proprietary cell balancing technique that continuously monitors and adjusts individual cell voltages, ensuring that each cell contributes equally to the pack's overall performance. This level of precision helps maintain battery health and extends the usable life of the pack.
State of charge (SOC) and state of health (SOH) estimation algorithms
Accurate estimation of a battery's state of charge (SOC) and state of health (SOH) is crucial for providing reliable range estimates and managing battery performance. Advanced BMS systems use complex algorithms that take into account factors such as temperature, voltage, and current to provide highly accurate SOC and SOH estimates.
These algorithms are constantly being refined to improve accuracy. For instance, some systems now incorporate machine learning techniques to adapt their estimations based on individual driving patterns and battery degradation over time.
Over-the-air BMS updates: Tesla's approach
Tesla has pioneered the use of over-the-air (OTA) updates for its vehicles, including updates to the battery management system. This approach allows for continuous improvement of battery performance and efficiency without requiring physical modifications to the vehicle.
Through OTA updates, Tesla has been able to increase the range of existing vehicles, improve charging speeds, and enhance battery longevity. This demonstrates the potential for software-based improvements to significantly impact EV performance long after the vehicle has left the factory.
Cost reduction strategies for lithium batteries in mass-market EVs
As electric vehicles transition from niche products to mass-market options, reducing the cost of lithium batteries becomes increasingly critical. Manufacturers are employing various strategies to drive down costs without compromising performance.
Economies of scale: gigafactories and vertical integration
One of the most effective ways to reduce battery costs is through economies of scale. Tesla's Gigafactories epitomize this approach, with massive production facilities designed to churn out batteries at an unprecedented scale. This not only reduces manufacturing costs but also allows for greater control over the supply chain.
Other manufacturers are following suit, with companies like Volkswagen and GM investing heavily in their own battery production facilities. This vertical integration helps reduce costs and ensures a stable supply of batteries as EV production ramps up.
Alternative cathode materials: sodium-ion technology
While lithium-ion batteries currently dominate the EV market, researchers are exploring alternative technologies that could offer cost advantages. Sodium-ion batteries, which use abundant and inexpensive sodium instead of lithium, are one promising avenue.
Companies like CATL are already developing sodium-ion batteries for use in electric vehicles. While these batteries currently offer lower energy density than lithium-ion, they have the potential to be significantly cheaper and could find applications in urban EVs or energy storage systems.
Structural battery packs: reducing vehicle weight and cost
Innovative designs that integrate the battery pack into the vehicle's structure offer another pathway to cost reduction. Tesla's structural battery pack, introduced with the 4680 cells, exemplifies this approach. By using the battery pack as a structural element, manufacturers can reduce the overall weight of the vehicle and simplify production.
This integration not only reduces material costs but also improves vehicle performance by lowering weight. As this technology matures, it has the potential to significantly impact the cost and efficiency of electric vehicles across the industry.